TAKEAWAY: The CSA Group is a standards organization that develops standards in several areas, including respirator selection, care, use, and testing. Formerly known as the Canadian Standards Association (CSA), the CSA Group is integral to SureHire’s Respirator-Fit Testing program.
Table of contents
- What is the CSA Group?
- Why are standards required for respirators, and what role do different organizations play?
- What are the CSA Group standards for respirators?
- What are the CSA Group standards for Respirator-Fit Testing?
- CSA Group and Respirator-Fit Testing | In Conclusion
- You May Also Be Interested In…
In conjunction with NIOSH, OSHA, and OHS, the CSA Group forms part of the framework for how SureHire conducts Respirator-Fit Testing. This article is the third and final part of our series decoding these acronyms. Read on to find out what CSA does and its role in Respirator-Fit Testing.
[Find out all about NIOSH in “What is NIOSH and Why is it Important for Respirator Fit Testing?”]What is the CSA Group?
The CSA Group is a global leader in standards development, testing, inspection, and certification. Their primary aims are to enhance public safety, improve the quality of life, preserve the environment, and facilitate trade.
CSA Group started as the Canadian Engineering Standards Association (CESA) as the first Canadian organization to develop commercial and industrial standards exclusively. In 1944 it became CSA, and in 2012, the CSA Group better reflected its scope.
The CSA Group develops and administers standards in a broad selection of industry sectors. These include health and safety, electronic, business management systems, construction, sustainability, etc.
CSA Group is an independent, not-for-profit organization recognized by the Occupational Safety and Health Administration (OSHA) as a Nationally Recognized Testing Laboratory (NRTL).
Anyone can submit a proposal to request a standard from CSA Group. For example, a government department or consumer organization may see a need for a standard that they’ll put forward for the CSA Group to consider.
Why are standards required for respirators, and what role do different organizations play?
Respiratory Protective Equipment (RPE) is an essential health and safety consideration for many industries and job roles. It helps minimize the chance of inhaling dangerous substances and reduces the risk of respiratory conditions, ultimately helping keep workers safe and well.
Standards are crucial to ensure respirators meet minimum safety and quality requirements. They are also imperative for RPE use, such as SureHire’s Respirator-Fit Testing program. A respirator that meets health and safety standards is one part of the equation, and correct fit and use are another.
Several industries come together in various aspects of respirator health and safety. For example, the Centers for Disease Control and Prevention (CDC) sets performance criteria for respirators, and the National Institute for Occupational Safety and Health (NIOSH) tests and certifies respirators.
The Occupational Safety and Health Administration (OSHA) sets respirator safety standards and provides guidance and training. OSHA standards are enforceable by U.S. law. CSA Group standards are generally consistent but go into greater detail than OSHA standards.
Companies and organizations can purchase relevant occupational health and safety-related standards from CSA, such as maintenance of electrical systems, full-body harnesses, and selection, care, and use of respirators.
What are the CSA Group standards for respirators?
CSA Group standards are regularly reviewed and refreshed in line with requirements and technology development. Each standard is revised every five years, at a minimum.
CSA Group respirator standards specify that respirator selection is based on workplace hazards, current regulatory guidelines, and manufacturer information. A hazard assessment covers aspects such as the presence of contaminants and their source, acceptable exposure limits, signs and symptoms of irritation, and how dangerous they are.
What are the CSA Group standards for Respirator-Fit Testing?
Respirator-Fit Testing (also known as Mask-Fit Testing) ensures the respirator is the right fit for the person and worn correctly. SureHire’s Respirator-Fit Testing program follows the CSA group standards for respirator-fit testing, including the following.
When to test
Respirator-fit testing must be carried out at least every two years. Although this is the minimum requirement, industry bodies may recommend or require annual testing.
Employers should arrange testing after user screening, during or after training, and before using a respirator. It is also necessary to carry out Respirator-Fit Testing for any replacement respirator or when the person’s physical condition changes if it could affect the respirator fit.
Type of test
CSA Group standards allow a qualitative or quantitative mask-fit test. A qualitative test relies on taste or smell to detect leakage or a tight fit. Quantitative tests use specific equipment to test the respirator, which is considered the gold standard. SureHire uses the OSHA-compliant Portacount Pro Respirator Fit Tester as a quantitative testing method, reverting to qualitative testing at partner locations where it’s not available.
Personal testing considerations
The CSA Group standards require that the person testing the mask is clean-shaven in the area where the mask seals to the skin. Small patches of short facial hair that don’t interfere with the sealing surface may be acceptable. However, a clean-shaven policy is a more straightforward assurance that testing will be accurate. Although hair growth rate varies, this often requires the person to shave 12-24 hours before testing.
Accessories mustn’t affect the respirator fit. Items such as facial jewelry and head coverings must not come between the mask and seal, and the person should present themself in the same physical condition as when they’ll wear the respirator. Considerations for respirator fit include hairstyles and glasses or contact lenses. Make-up and lotions can also affect respirator effectiveness.
CSA Group and Respirator-Fit Testing | In Conclusion
OSHA recognizes the CSA Group to set standards across various industries and sectors. They provide standards for respirators and respirator-fit testing, with which SureHire complies.
Employees in industries with a high risk of lung health issues should invest in Respirator-Fit Testing to protect employees fully. Not only is it imperative to select a respirator that meets minimum safety requirements, but it’s also crucial to select one that fits the user correctly.
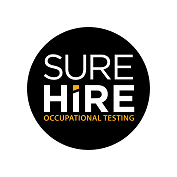
Contact us for more information about lung health testing services such as Respirator-Fit Testing, Spirometry Testing, Lead Exposure and Health Monitoring, and Lung Health Monitoring programs.
You May Also Be Interested In…
- Do You Have Reasonable Suspicion?Employers cannot initiate reasonable suspicion testing without first going through the 5-step process. Reasonable suspicion training provides critical information about how to initiate reasonable suspicion testing, including the 5-step process and other tools that employers can use to help manage the misuse of alcohol and drugs in the workplace.
- An Employer’s Guide: What You and Your Employees Need to Know About DOT Drug & Alcohol TestingWhen implementing or maintaining DOT Drug & Alcohol testing, there are key areas that employers should consider.
- SureHire Occupational Testing Acquires COHR Health: A Positive Step Towards Safe, Healthy, Productive Workforces and CommunitiesWe are thrilled to announce that today, May 6, 2024, SureHire Occupational Testing has officially acquired COHR Health, a well-known leader in occupational health services. Read on…
- Occupational Testing Use Case – MiningIn this case study, we will explore how mining companies can use various types of occupational tests to reduce Total Recordable Incident Rates (TRIR) long term.
- 9 Strategies to Keep Workers Cool on Drilling Sites During Hot Summer MonthsThis article delves into strategies to keep workers cool and safe on drilling sites during the hot summer months.
- Hearing Conservation Basics: How to Manage Occupational NoiseLearn how to proactively mitigate occupational noise risks and help prevent NIHL among workers.