TAKEAWAY: This article is the first in a 5-part series on the increased risks of noise-induced hearing loss (NIHL) in various industries. It examines the noise-related risks workers in the oil and gas industry face, comparisons with other sectors, and employer obligations for protecting their workforce from workplace-related NIHL.
Jump Ahead
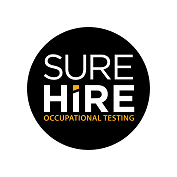
Request a Quote Today!
SureHire offers Audiometric Testing both in-facility and through our mobile fleet. Contact us today to request a quote!
Noise is among the most common occupational hazards, and occupational hearing loss is one of the most frequent work-related illnesses in North America. Workers in the oil and gas industry have a high risk of noise exposure, but there are several steps employers can take to mitigate this risk.
Any sound can be a hazard if it is loud enough or if a person is exposed to significant noise for long and often enough. When noise exposure exceeds recommended levels, it can damage hearing permanently.
Noise risks in the oil and gas industry
The 4 phases of oil and gas development are drilling, hydraulic fracturing, completion, and development. Studies show noise levels at each stage often exceed permissible commercial and residential levels. Drilling, fracturing, compressors, vehicle noise, venting, and flaring all contribute to excessive noise levels in the oil and gas industry.
Noise from the oil and gas industry affects workers and nearby residential populations. A scientific literature review on environmental noise exposure from the oil and gas industry showed a relationship with adverse public health outcomes. The study highlighted that oil and gas activities produce noise at levels that can negatively affect health aspects such as sleep quality and cardiovascular disease.
If the industry noise affects those residing near the operation, then it’s clear that noise can affect on-site workers even more if they are not adequately protected.
Oilfield worker noise risks compared to other safety-sensitive industries
NIHL is common in several industries, including manufacturing, forestry and agriculture, transportation, and mining. NIHL research in the oil and gas industry shows a high risk for workers compared with many other sectors.
A study on hearing loss in noise-exposed workers compared the audiograms of 1.9 million workers across all industries. The mining and oil and gas extraction (OGE) industries had a significantly higher prevalence of hearing loss than other industries. Mining came in the highest at 24 percent and OGE second with a 14 percent prevalence.
All other industries combined came out at 16 percent. Some mining and OGE subsectors exceeded these prevalences. The study results highlight the high-risk level for oilfield workers compared to other industries because mining was the only industry with higher noise risks.
A report from the Centers for Disease Control and Prevention (CDC) highlighted that nearly 17 percent of mining, quarrying, and OGE workers had some hearing impairment. This percentage was similar to the construction industry and higher than all other industries. Because the report grouped OGE with mining and quarrying, it’s not possible to look at OGE hearing loss alone compared with other industries in this instance.
The National Institute for Occupational Safety and Health (NIOSH) analyzed data on workplace noise exposure and the use of Hearing Protection Devices (HPDs). Workplace noise exposure was highest in mining, followed by lumbar and wood manufacturing. Repair and maintenance, motor vehicle operators, and construction trades were high-risk occupations.
Common signs of hearing loss
Some of the most common initial signs of hearing loss include the following:
- Difficulty hearing others speak, especially women and children
- Asking people to repeat themselves
- Favoring one ear over the other
- A ringing sensation in one or both ears
- Others comment that you seem to have difficulty hearing
Employers should take a proactive approach to avoid NIHL. Both employers and employees should be aware of the initial warning signs of NIHL. This awareness enables the implementation of an early intervention to prevent further hearing loss.
Employer obligations
Employers can help prevent occupational hearing loss in the oil and gas industry in several ways. Examples of preventative measures and early intervention steps employers can take to help protect their employees include the following.
Employer education around noise exposure and regulations
Employers must understand provincial and federal laws for noise exposure. These can and do change over time, and employers must stay up to date with current industry and regional regulations.
Specifications usually highlight the maximum exposure duration for each noise level. For example, in most jurisdictions, the allowable steady noise level for an entire eight-hour work shift is 85 A-weighted decibels (dBA). Federal regulations are slightly higher, as are those in Quebec.
For each decibel above the limit, employers must decrease employee exposure time.
Invest in noise-reducing equipment
Alongside provincial, state, and federal industry noise regulations, employers can use noise-reducing equipment relevant to the oil and gas industry, including the following:
- Portable noise screens to reduce drilling noise
- A fully-enclosed sound-attenuated building or an absorptive noise barrier to reduce noise from natural gas compressors
- Other sound barriers made from steel and sound-absorbing insulation around additional noise-hazard facilities
- Engine mufflers
- Replace older equipment with quieter modern equivalents. For example, replace natural gas or diesel motors with electric ones and replace fan blades when needed.
Develop new noise-related procedures
Employers can take steps to reduce noise exposure for oil and gas workers by making environmental and procedure adjustments. Examples include:
- Providing quiet areas
- Restricting worker proximity to noise sources
- Limiting time spent in noisy areas
- Creating appropriate designated times for noisy activities
Invest in Personal Protective Equipment (PPE) for employees
Employers must supply appropriate Personal Protective Equipment (PPE) for employees exposed to high noise levels. Custom-molded earplugs or earmuffs can help protect employees from NIHL.
Audiometric testing
A robust health and safety program combined with occupational testing can help contribute to safer workplaces in the oil and gas industry. Audiometric testing is one of the occupational testing services critical to this industry. As well as crucial, it’s a sometimes mandatory tool for detecting and preventing hearing loss.
Employers can also use baseline and periodic hearing tests that measure a person’s ability to hear sounds at different pitches and intensities. SureHire offers mobile, on-site hearing testing services for greater ease of testing and reduced downtime.
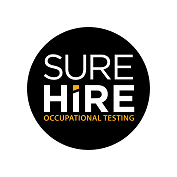
Need Testing in the U.S.? Connect with our team today!
SureHire USA offers Audiometric Testing through our extensive network of facilities. Contact us today to request a quote!
You May Also Be Interested In…
- Do You Have Reasonable Suspicion?Employers cannot initiate reasonable suspicion testing without first going through the 5-step process. Reasonable suspicion training provides critical information about how to initiate reasonable suspicion testing, including the 5-step process and other tools that employers can use to help manage the misuse of alcohol and drugs in the workplace.
- An Employer’s Guide: What You and Your Employees Need to Know About DOT Drug & Alcohol TestingWhen implementing or maintaining DOT Drug & Alcohol testing, there are key areas that employers should consider.
- SureHire Occupational Testing Acquires COHR Health: A Positive Step Towards Safe, Healthy, Productive Workforces and CommunitiesWe are thrilled to announce that today, May 6, 2024, SureHire Occupational Testing has officially acquired COHR Health, a well-known leader in occupational health services. Read on…
- Occupational Testing Use Case – MiningIn this case study, we will explore how mining companies can use various types of occupational tests to reduce Total Recordable Incident Rates (TRIR) long term.
- 9 Strategies to Keep Workers Cool on Drilling Sites During Hot Summer MonthsThis article delves into strategies to keep workers cool and safe on drilling sites during the hot summer months.
- Hearing Conservation Basics: How to Manage Occupational NoiseLearn how to proactively mitigate occupational noise risks and help prevent NIHL among workers.