TAKEAWAY: Research, accident investigations, and analyses regularly identify non-compliance as a significant contributor to accidents, including those in the oil and gas industry. Occupational testing, alongside a robust health and safety program, can help.
Jump Ahead
The Oil and Gas industry can be a dangerous business. Oilfield workers are susceptible to wide-ranging injuries and fatalities, including slips and falls, gas poisoning, electrocution, and explosion. Many of these accidents are the result of human error. These workers can also be at increased risk for hearing loss and lung issues due to the nature of the work and the substances they must work with.
However, despite the many dangers inherent in the industry, a focus on safety has driven huge improvements that better protect its workers. In the U.K., fatalities in the sector dropped by 76% from 2007 to 2018. Over the last 20 years, fatalities have been reduced by 70% in Canada. Similar numbers have been reported worldwide despite an increase in the overall number of hours worked by employees.
Still, oil and gas industries have a high social and economic cost. In fact, research, accident investigations, and analyses regularly identify non-compliance as a significant contributor to accidents, including those in the oil and gas industry. Occupational testing, alongside a robust health and safety program, can help.
Health and Safety Programs
Major oil and gas companies, including Shell, are acknowledging the dangerous work their people do and renewing efforts to increase safety in their workplaces. This includes an increased commitment to health and safety training. Research suggests that health and safety education can help keep workers safe and improve employee performance. A recent study of Nigerian oil and gas workers, for example, established a significant and positive relationship between training and performance. Research on Malaysian oil and gas workers also provided a strong correlation between increased health and safety training and reduced accidents.
Health and safety training should focus on knowledge and risk mitigation but also on promoting continual awareness of those risks. In Houston, a study found that mindfulness increased situational awareness and productivity in oil and gas workers. Perhaps more importantly, these workers were also found to experience less fatigue and emotional and psychological strain, all of which can contribute to accidents and injuries.
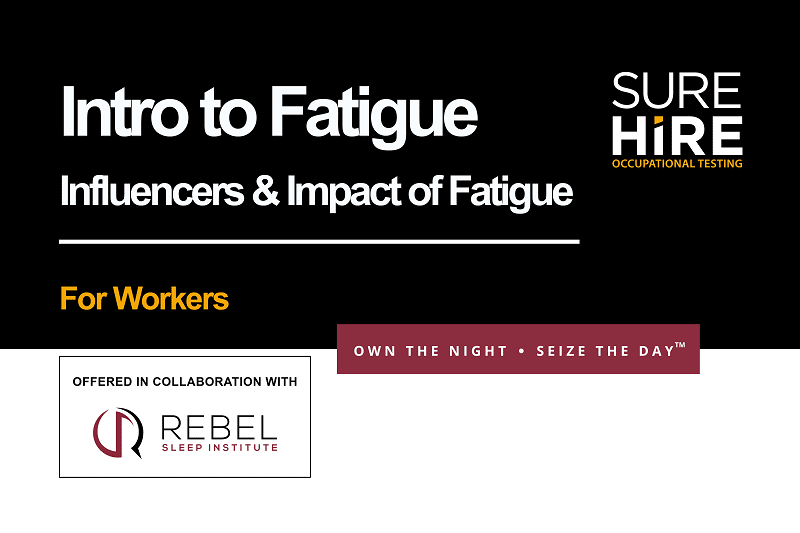
30-Minute Micro-Module: Influencers and Impacts of Fatigue
Fatigue is a direct well-known contributor to motor vehicle and workplace accidents resulting in injury and death. Prevention begins with educating your workforce!
Learn more about our 30-minute micro-module and register online today.
However, research also suggests that training alone is insufficient to mitigate risks and reduce accidents. Accident investigations and analyses regularly identify non-compliance as a significant contributor to accidents, including in the oil and gas industry. That, conclude researchers, requires governance initiatives that enforce strict adherence to correct safety procedures. And this is what occupational testing can help ensure.
Drug and Alcohol Testing
Drug and alcohol testing is critical in the oil and gas industry. In fact, it is mandated under the Pipeline and Hazardous Materials Safety Administration (PHMSA) and Department of Transportation (DOT) regulations in the U.S. Even in Canada, where existing laws result in more tightly controlled drug testing, some agencies and many companies are implementing drug testing aimed at reducing preventable accidents and ensuring worker and public safety.
Recent research supports this approach. For example, a new study on Canadian oil and gas workers suggests that testing be undertaken to prevent injuries in this field, including promoting and supporting drug-free programmes, given the rate of positive alcohol screening in this population. This approach continues to make sense given the increased use of illicit drugs in general among North American workers.
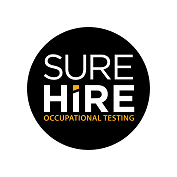
Request a Quote Today!
SureHire’s drug and alcohol testing services help employers manage the risk of workplace substance abuse, incidents, costly WCB claims, as well as the successful rehabilitation of employees in need of drug and alcohol abuse support programs.
Audiometry Testing
Occupational testing should, however, also focus on identifying and preventing injuries that may occur over time. A study of U.S. oil and gas workers concluded that these workers were at a much higher risk for hearing loss than workers in many other industries due to exposure to noise and toxic chemicals. The study recommended employers pay critical attention to conserving workers’ hearing and maintaining their quality of life. This same study pegged the prevalence of hearing loss in oil and gas workers at 14%.
Ongoing audiometry testing that includes a baseline reading done within six months of employment can help identify and prevent hearing loss in oil and gas workers. The results of these tests can also induce compliance with company and industry rules around wearing appropriate personal protective equipment (PPE) and other safety measures. The CDC recommends audiometric testing, and in one study, annual testing led over half of the participants to change their habits at work and home and improved their job and home hearing protection use.
Fit Testing
Fit testing can also aid employers in reducing injury in the oil and gas industry. Of course, fit testing of hearing protection-related PPE is essential. However, it is equally critical to protect workers from the deadly gases they work with. Hydrogen sulphide (H2S) is one of those gases. It can cause discomfort and dizziness at a low level, but at higher levels, it can lead to unconsciousness and death within minutes. It is an ever-present danger during crude oil drilling and gas extraction. Researchers point out that the only protections in these environments are breathing protection solutions with a demonstrably secure seal and minimal leakage. This requires ongoing respirator fit testing for workers.
While H2S is perhaps the most prevalent threat to oil and gas workers, it is not the only one. Most major industry organizations promote regular fit testing as part of their health and safety recommendations.
Fit for Duty Testing
Musculoskeletal disorders (MSDs) are also, unfortunately, common among oil and gas industry workers. While identifying potential hazards is a crucial best practice, it’s equally important that employees are ready and able to handle the job’s physical demands. This is especially true in oil and gas, a physically demanding job, often requiring workers to work in tight or uncomfortable spaces and frequently perform repetitive tasks. Age and physical condition can put these workers at increased risk. Fit for duty (also know as fitness-to-work) testing can help reduce MSDs by ensuring a worker’s physical capabilities can meet the requirements of the job.
You May Also Be Interested In…
- Do You Have Reasonable Suspicion?Employers cannot initiate reasonable suspicion testing without first going through the 5-step process. Reasonable suspicion training provides critical information about how to initiate reasonable suspicion testing, including the 5-step process and other tools that employers can use to help manage the misuse of alcohol and drugs in the workplace.
- An Employer’s Guide: What You and Your Employees Need to Know About DOT Drug & Alcohol TestingWhen implementing or maintaining DOT Drug & Alcohol testing, there are key areas that employers should consider.
- SureHire Occupational Testing Acquires COHR Health: A Positive Step Towards Safe, Healthy, Productive Workforces and CommunitiesWe are thrilled to announce that today, May 6, 2024, SureHire Occupational Testing has officially acquired COHR Health, a well-known leader in occupational health services. Read on…
- Occupational Testing Use Case – MiningIn this case study, we will explore how mining companies can use various types of occupational tests to reduce Total Recordable Incident Rates (TRIR) long term.
- 9 Strategies to Keep Workers Cool on Drilling Sites During Hot Summer MonthsThis article delves into strategies to keep workers cool and safe on drilling sites during the hot summer months.
- Hearing Conservation Basics: How to Manage Occupational NoiseLearn how to proactively mitigate occupational noise risks and help prevent NIHL among workers.