TAKEAWAY: This article is the final in a 5-part series about NIHL in high-risk industries. Read on to learn about NIHL risks in manufacturing and how employers can help protect their workers.
Jump Ahead
Loud sounds in and outside the workplace can put a person at risk of noise-induced hearing loss (NIHL). However, noise in the workplace setting is a more significant problem, especially for workers in high-risk industries. The manufacturing industry is one of several sectors with a high risk of occupational noise-induced hearing loss (ONIHL), so employers must take the necessary steps to protect their employees.
In industries such as mining, agriculture, and oil and gas, employees are at a high risk of exposure to noise loud enough to cause hearing damage. Noise-induced hearing loss can come from a single loud source, such as an explosion or exposure over time. Employers should also recognize that employees are exposed to loud sounds outside the workplace. Therefore, a conservative approach toward minimizing the risks is best.
Noise risks in the manufacturing industry
According to the Centers for Disease Control and Prevention (CDC), around 46 percent of manufacturing workers have been exposed to hazardous noise. Approximately 18 percent of workers in this sector have hearing difficulty, and 11 percent have tinnitus.
A CDC report highlighted that close to 14 percent of manufacturing workers had some degree of hearing loss. This figure is slightly lower than the mining industry (at 16 percent) but higher than other high-risk sectors, such as agriculture and farming (11 percent) and transportation (just under eight percent).
A study on noise risks for manufacturing workers in Malaysia concluded that all workforces had a high risk of noise exposure. The metal, textile, and food industries were among the highest. Other data highlights that wood product manufacturing is another high-risk sector.
Manufacturing workers are exposed to several noises loud enough to put a worker at risk of NIHL. Significant noise sources include compressors, pumps, motors, fans, turbines, vents, steam leaks, and control valves.
How manufacturing employers can reduce noise exposure in the workplace
NIHL is permanent and irreversible. Therefore, employers should take every possible step toward minimizing the risks and protecting workers. The following actions offer guidance to get started and can also help prevent further hearing loss in workers with NIHL.
1. Understand the signs and symptoms of hearing loss
NIHL is one of the most common yet preventable work-related health problems. Understanding the warning signs of NIHL can help employers take action to create an early intervention plan. Common indications of hearing loss include:
- A ringing sound in one or both ears
- Asking people to repeat things they’ve said because you couldn’t hear them properly
- Muffled hearing or noticing temporary hearing loss at the end of a workday
2. Use audiometric testing to measure hearing loss
Audiometric testing is a reliable method for detecting hearing loss. Employers should provide baseline and periodic hearing tests to measure hearing loss. Doing so enables them to make the best decisions to protect their workers’ health.
Hearing tests measure how well a person can hear sounds at different pitches and intensities. Testing is not only recommended but often mandatory and is a vital step toward keeping workers safe. Employers can choose mobile testing for a convenient and time-efficient solution.
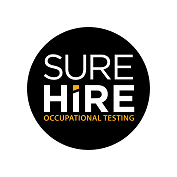
Book Audiometric Testing for your Workforce Today!
With over 6,500 locations across North America, SureHire can support your testing needs. Contact us to speak with a member of our team and request a quote today!
3. Understand noise exposure limits
Subjective and objective measures can help determine whether workplace noise levels are problematic. Simple observations such as needing to raise your voice when speaking to someone close by can indicate that noise is above an acceptable level.
Employers must also understand objective measures for noise exposure. These limits can and do change over time, so it’s crucial to stay up-to-date with federal and regional laws, plus any industry guidelines.
The noise limit in most jurisdictions is 85 A-weighted decibels dB(A) over an eight-hour day. When sounds louder than 85 dB(A) are present in the workplace, the exposure time must be reduced accordingly.
4. Assess workplace noise exposure
Employers can use audiometric questionnaires to understand worker noise exposure from work and leisure over their lifetime.
Similarly, a noise-specific workplace hazard assessment can provide insights into daily noise exposure. To measure noise exposure, employers must obtain information about noise levels emitted from different machinery and make calculations based on exposure time.
5. Adjust workplace processes to reduce risk
Wherever possible, employers can adapt the workplace layout and modify job task procedures to reduce noise exposure. Examples include:
- Place noisy machinery as far away from workers as possible, in an enclosed room, if feasible
- Create a well-designed job rotation plan to limit the time each worker spends in a noisy area
- Provide ongoing education and training for employees on how to use equipment properly and follow hearing-safe practices
6. Invest in noise-reducing equipment or modify existing equipment
Employers can purchase quieter, modern equipment to lower workplace noise levels. Or invest in additional parts designed to reduce the noise of existing equipment. Examples include:
- Barriers for sound-insulation to act as a noise-enclosure
- Machine mountings to reduce vibration levels
- Using noise-dampening materials for guards and panels
- Installing silencers to exhaust systems
Clean and service all equipment regularly to help ensure it maintains noise-reduction capabilities.
When working near noisy machinery is unavoidable, employees should use earmuffs or custom-molded earplugs to help protect their hearing. It is crucial to ensure any hearing protection fits well and that employees know how to use it properly.
NIHL in the manufacturing industry | In conclusion
Manufacturing is one of several high-risk industries for NIHL. It’s a widespread yet preventable problem, and employers can reduce the risks of ONIHL in several ways. Both employers and employees must be educated on avoiding NIHL, such as using appropriate hearing protection and minimizing exposure to loud noises.
Where hearing loss is already an issue, employers can find out how to accommodate deaf and hard-of-hearing employees.
For further reading about the manufacturing industry, find out about the most common musculoskeletal injuries in this sector and preventative tips to keep your workforce safe.
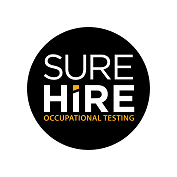
Book Audiometric Testing for your Workforce Today!
With over 6,500 locations across North America, SureHire can support your testing needs. Contact us to speak with a member of our team and request a quote today!
You May Also Be Interested In…
- Do You Have Reasonable Suspicion?Employers cannot initiate reasonable suspicion testing without first going through the 5-step process. Reasonable suspicion training provides critical information about how to initiate reasonable suspicion testing, including the 5-step process and other tools that employers can use to help manage the misuse of alcohol and drugs in the workplace.
- An Employer’s Guide: What You and Your Employees Need to Know About DOT Drug & Alcohol TestingWhen implementing or maintaining DOT Drug & Alcohol testing, there are key areas that employers should consider.
- SureHire Occupational Testing Acquires COHR Health: A Positive Step Towards Safe, Healthy, Productive Workforces and CommunitiesWe are thrilled to announce that today, May 6, 2024, SureHire Occupational Testing has officially acquired COHR Health, a well-known leader in occupational health services. Read on…
- Occupational Testing Use Case – MiningIn this case study, we will explore how mining companies can use various types of occupational tests to reduce Total Recordable Incident Rates (TRIR) long term.
- 9 Strategies to Keep Workers Cool on Drilling Sites During Hot Summer MonthsThis article delves into strategies to keep workers cool and safe on drilling sites during the hot summer months.
- Hearing Conservation Basics: How to Manage Occupational NoiseLearn how to proactively mitigate occupational noise risks and help prevent NIHL among workers.
7 Occupations with Highest Reported Cases of Hearing Loss
[…] and Health (NIOSH), approximately 17% of workers in the manufacturing sector have hearing loss. Manufacturing workers are exposed to loud noise from machinery and equipment used in the production process, such as saws […]