TAKEAWAY: Get an overview of safety training requirements in Canada and the United States and highlight some essential resources to help you meet those requirements.
Jump Ahead
The construction industry is one of the most hazardous industries in Canada and the United States, with a high number of accidents and fatalities occurring each year. In fact, according to the National Safety Council, the construction industry is one of the most dangerous, experiencing more worker deaths each year than any other industry. To prevent these accidents, both countries have established safety training requirements for workers in the construction industry.
Safety Training Requirements in Canada
In Canada, the federal government and each province have regulations for construction safety training. At a minimum, Canadian employers must provide training that includes an overview and the employee’s three basic rights in federal jurisdiction, details about the health and safety committee, workplace inspections, hazard prevention and violence prevention programs, and accident investigation. However, all Canadian jurisdictions also require employers to provide workers with training in the following areas:
1. Fall Protection
Workers must be trained in fall protection systems and equipment, including personal protective equipment (PPE), guardrails, and safety nets. This should also include training about the fall-protection plan and emergency procedures if there is a risk of drowning.
2. Hazard Communication
Workers must be trained in identifying and communicating hazards in the workplace, including chemical, physical, and biological hazards. Specific training is usually required for many risks, including asbestos, compressed air, carbon monoxide and chainsaws.
3. Personal Protective Equipment (PPE)
Workers must be trained on the proper selection of PPE, including hands-on instruction in the fit, use and maintenance of assigned PPE. They must also be trained in the limitations of PPE, what to do when devices fail, and when they need to be replaced or discarded.
4. Confined Spaces
Workers must be trained on the hazards of working in confined spaces and the safe entry and exit procedures. This includes training on PPEs and the specific emergency procedures for the worksite.
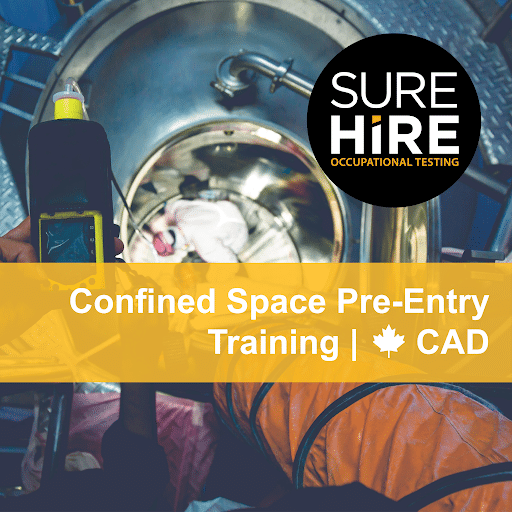
Educate Your Workforce!
The Confined Space Pre-Entry training course is designed in compliance with the Canada Labour Code (the Code) and Part XI (Confined Spaces) of the Canada Occupational Health and Safety Regulations (COHSR), including practices and procedures to protect workers from the hazards associated with working in confined spaces.
5. Electrical Safety
Workers must be trained on electrical safety procedures, including lockout and tag out procedures and safe work practices around electrical equipment. The Canadian Standards Association (CSA) CSA Z462 Workplace Electrical Safety Standard, 2021, also provides specific recommendations concerning electrical training.
6. Respiratory Protection
Workers must be trained on properly using and maintaining respiratory protection equipment. Mask fit testing is required as part of this training every two years and is recommended annually.
Safety Training Requirements in the United States
In the United States, the Occupational Safety and Health Administration (OSHA) sets safety training requirements for workers in the construction industry. Many states also have additional regulations that enhance the OSHA regulations. OSHA requires that employers provide workers with training in the following areas:
1. Fall Protection
Workers must be trained in fall protection systems and equipment, including PPE, guardrails, safety nets, and other fall protection systems. Training must be conducted by a trained professional and include training on recognizing and mitigating common fall hazards.
2. Hazard Communication
Workers must be trained in identifying and communicating hazards in the workplace, including chemical, physical, and biological hazards. Employers are also expected to disclose hazards that are present in the workplace to their employees, and there are specific training requirements for substances such as asbestos.
3. Personal Protective Equipment
Workers must be trained on the proper selection, use, and maintenance of PPE. They must also be trained in the limitations of PPE, what to do when devices fail, and when they need to be replaced or discarded.
4. Confined Spaces
Workers must be trained on the hazards of working in confined spaces and the safe entry and exit procedures. This includes training on PPE and emergency procedures and requirements for additional training if the employee indicates a lack of compliance.
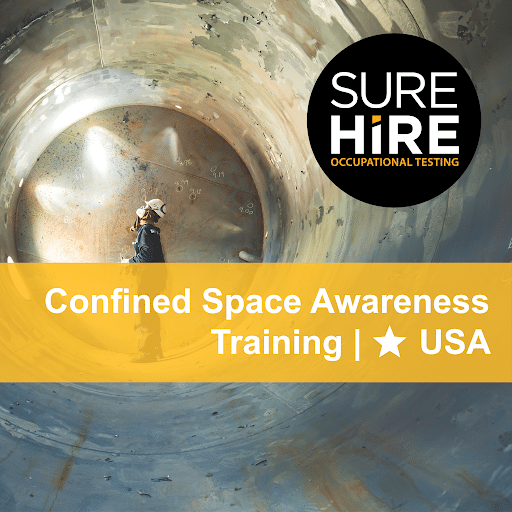
Educate Your Workforce!
The Confined Space Awareness training course is designed in compliance with the OSHA Confined Space Awareness Training requirements as outlined in the Title 29 CFR 1910.146, including practices and procedures to protect workers from the hazards associated with working in confined spaces.
5. Electrical Safety
Workers must be trained on electrical safety procedures, including lockout/tagout procedures and safe work practices around electrical equipment. The level of training is determined by the risk profile of the worker and can be on-the-job or classroom-based.
6. Respiratory Protection
Workers must be trained on properly using and maintaining respiratory protection equipment, including mask fit and emergency procedures.
7. Scaffolding
Workers who use scaffolding must be trained in the hazards associated with scaffolding and the proper procedures for setting up and using scaffolding. A trained professional focusing must conduct training on recognizing and controlling risks.
In Canada and the United States, safety training requirements for workers in the construction industry are designed to prevent accidents and fatalities. These requirements cover various topics, including fall protection, hazard communication, personal protective equipment, confined spaces, electrical safety, respiratory protection, and scaffolding. Employers can create a safe and healthy workplace and reduce the risk of accidents and injuries by providing workers with the necessary training.
Additional Resources on Safety Training in North America
The Canada Occupational Health and Safety Regulations list the legal requirements for companies regarding safety training.
The Canadian Centre for Occupational Health and Safety is a government-run site that provides a wealth of information on safety training.
The Occupational Health and Safety Administration site, run by the U.S. Department of Labor has a wealth of information about regulations and safety training.
You May Also Be Interested In…
- Do You Have Reasonable Suspicion?Employers cannot initiate reasonable suspicion testing without first going through the 5-step process. Reasonable suspicion training provides critical information about how to initiate reasonable suspicion testing, including the 5-step process and other tools that employers can use to help manage the misuse of alcohol and drugs in the workplace.
- An Employer’s Guide: What You and Your Employees Need to Know About DOT Drug & Alcohol TestingWhen implementing or maintaining DOT Drug & Alcohol testing, there are key areas that employers should consider.
- SureHire Occupational Testing Acquires COHR Health: A Positive Step Towards Safe, Healthy, Productive Workforces and CommunitiesWe are thrilled to announce that today, May 6, 2024, SureHire Occupational Testing has officially acquired COHR Health, a well-known leader in occupational health services. Read on…
- Occupational Testing Use Case – MiningIn this case study, we will explore how mining companies can use various types of occupational tests to reduce Total Recordable Incident Rates (TRIR) long term.
- 9 Strategies to Keep Workers Cool on Drilling Sites During Hot Summer MonthsThis article delves into strategies to keep workers cool and safe on drilling sites during the hot summer months.
- Hearing Conservation Basics: How to Manage Occupational NoiseLearn how to proactively mitigate occupational noise risks and help prevent NIHL among workers.