TAKEAWAY: In this blog post, we’ll provide an overview of the safety training requirements in the mining industry and highlight some essential resources to help you meet your obligations.
Jump Ahead
Safety is paramount in the mining industry. Mining is one of the most dangerous job sectors where workers have a high risk of work-related injuries and fatalities. Mining industry employers must be familiar with the safety training requirements in their state or province to ensure safety on their work sites.
Why is safety training vital for the mining industry?
The mining industry faces several unique safety-related challenges. Mining industry employers should have safety at the forefront of their organization for several reasons:
- Mining industry employees are at risk of noise-induced hearing loss
Mining is a high-risk sector for noise-induced hearing loss (NIHL). Mine industry employees are exposed to loud noises from various sources and processes. Employers can take steps to reduce noise to safe levels, such as investing in noise-reducing equipment and personal protective equipment (PPE), such as custom-moulded ear plugs.
Employees should receive training related to NIHL to understand the risks of hazardous noise levels, how to reduce noise exposure, and how to properly use noise-related PPE.
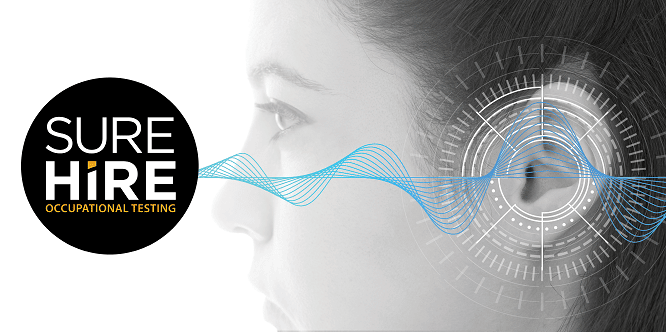
Book an Appointment Today!
SureHire’s audiometric testing services allow you to detect NIHL before it becomes a problem, providing you with the information you need for investigation and intervention so you can protect your workforce.
- Mine workers are exposed to dangerous substances
Mine workers are often exposed to substances like coal dust, which may damage their health. Coal dust can cause several severe respiratory conditions that employers must be aware of.
Employers can design safety training programs to educate employees on reducing their exposure to harmful substances.
- Mines may be in remote locations
Miners often work in remote areas, far from medical care. Therefore, employers must take steps to improve workplace health and safety. Should health and safety issues arise on the job site, employees should be well-versed in dealing with emergencies to help keep themselves and their coworkers safe.
- Safety training minimizes the risk of work-related musculoskeletal injuries
Several mining activities are associated with a high risk of musculoskeletal injuries. These include handling supplies or materials, getting on or off equipment or machines, machine maintenance and repair, and using hand tools.
Safety training is crucial for minimizing the risk of musculoskeletal injuries from such activities. For example, training in lifting techniques and how and when to distribute loads can reduce the incidence of back injuries, the most common injury site in miners.
Furthermore, workers must be trained to use equipment and tools safely. Employers can invest in state-of-the-art equipment, but it’s only worthwhile if workers know how to use it safely and effectively.
- Miners may be at high risk of opioid dependence
Mine industry workers may be at a high risk of injuries requiring an opioid prescription. Such prescriptions can lead to drug dependence or overdose.
Impairment training should be a part of any workplace alcohol and drug policy. It can help increase awareness and prevent dependence and overdose issues.
- Safety training reduces accident and fatality rates
Although mining is notoriously known as a dangerous industry, safety training helps reduce the incidence of workplace accidents through education and awareness. In turn, accident-related injury and fatality statistics also decline.
Safety training requirements in the mining industry
The Mine Safety and Health Administration (MSHA) is a branch of the US Department of Labor that oversees safety training requirements in the mining industry. Federal law specifies that miners must receive basic and annual refresher training. They also state that all mine operators must maintain an effective training plan.
The Federal code 30 CFR Part 48 covers all underground mining, plus surface mining of coal and some metals. Training plans and trainers must be MSHA-approved. Part 46 covers the aggregate industry, including granite, sand, gravel, lime, and cement operations. For Part 46, training plans and trainers do not require MSHA approval but must meet the rule’s requirements.
Federal involvement in mining is limited in Canada, and provincial governments are responsible for regulating mining within their jurisdiction.
The Mining Association of Canada is the voice of the Canadian mining industry. They offer several resources for mining employers and facilitate the Towards Sustainable Mining (TSM) program to support mining companies in environmental and social risk management.
Essential resources for mining industry employers
Mining industry employers can explore the resources available to them when building a safer, healthier workplace and workforce. Examples include the following:
- The MSHA offers various mine health and safety training programs. These include in-person and online courses. Examples of resources include the Miners’ Rights and Responsibilities online training program and the Miners’ Representatives Guide.
- The MSHA has several health and safety materials to promote safety in US mines. These include their Small Mine Guide, training videos, and handbook series.
- The MSHA also assists mining employers in developing a training plan, educates about mine rescue training, and offers free access to previous quarterly training conference calls and stakeholder meetings.
- The Colorado School of Mines and the Western Mining Safety and Health Training Resource Center provide MSHA Part 48 new miner training and annual refreshers.
- Employers can access several mining safety training programs to help ensure compliance with MSHA regulations. Many of these are free, app-based training programs with short, easy-to-digest content.
- The National Institute for Occupational Safety and Health (NIOSH) mining program aims to eliminate mining fatalities, injuries, and illnesses through relevant research and impactful solutions.
How mining industry employers can protect their employees
Mining industry employers can use the resources above to develop robust safety training plans. Employers can also invest in several safety-related occupational testing services relevant to mine workers to help protect their employees. Examples are as follows:
- Drug and alcohol testing services and Reasonable Suspicion Training (RST) can help raise employee awareness and reduce the incidence of substance abuse in the workplace.
- Audiometric testing services address the issue of NIHL and help keep workers safe through early detection of hearing problems and measuring changes over time.
- Mine workers often require lung health testing programs, including a health questionnaire, mask-fit testing, spirometry, and chest x-rays.
- Mining industry employers should ensure employees receive a complete medical exam to identify underlying health concerns since medical care is often far away. The knowledge obtained from these tests enables employers to establish an appropriate course of action to accommodate an employee’s health issues.
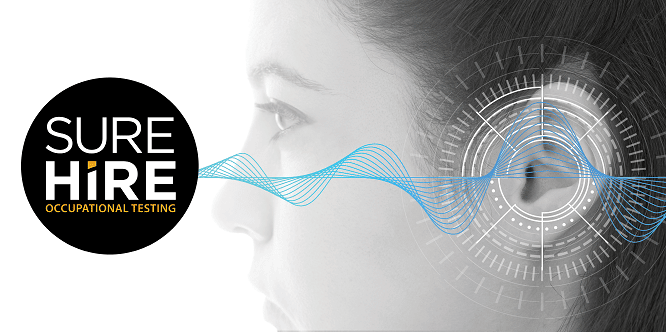
Book an Appointment Today!
SureHire’s audiometric testing services allow you to detect NIHL before it becomes a problem, providing you with the information you need for investigation and intervention so you can protect your workforce.
You May Also Be Interested In…
- Do You Have Reasonable Suspicion?Employers cannot initiate reasonable suspicion testing without first going through the 5-step process. Reasonable suspicion training provides critical information about how to initiate reasonable suspicion testing, including the 5-step process and other tools that employers can use to help manage the misuse of alcohol and drugs in the workplace.
- An Employer’s Guide: What You and Your Employees Need to Know About DOT Drug & Alcohol TestingWhen implementing or maintaining DOT Drug & Alcohol testing, there are key areas that employers should consider.
- SureHire Occupational Testing Acquires COHR Health: A Positive Step Towards Safe, Healthy, Productive Workforces and CommunitiesWe are thrilled to announce that today, May 6, 2024, SureHire Occupational Testing has officially acquired COHR Health, a well-known leader in occupational health services. Read on…
- Occupational Testing Use Case – MiningIn this case study, we will explore how mining companies can use various types of occupational tests to reduce Total Recordable Incident Rates (TRIR) long term.
- 9 Strategies to Keep Workers Cool on Drilling Sites During Hot Summer MonthsThis article delves into strategies to keep workers cool and safe on drilling sites during the hot summer months.
- Hearing Conservation Basics: How to Manage Occupational NoiseLearn how to proactively mitigate occupational noise risks and help prevent NIHL among workers.