TAKEAWAY: This article explores ways to manage occupational noise, no matter which industry you’re in. Read on to learn how to proactively mitigate occupational noise risks and help prevent NIHL among workers.
Jump Ahead
- Identify Noise-Related Hazards in the Workplace
- Conduct a Noise Assessment to Assess the Risks
- Engineering Controls: Equipment Modification or Replacement
- Administrative Controls: Adjusting Workplace Protocols and Procedures
- Use Hearing-Related Personal Protective Equipment (PPE)
- Conduct Regular Audiometric Testing
- Hearing Conservation Basics | In Conclusion
- You May Also Be Interested In…
The Centers for Disease Control (CDC) estimates that 22 million workers are exposed to potentially damaging noise annually, a problem that can have far-reaching adverse effects. High noise levels may interfere with workplace communication and, in turn, increase the risk of related accidents and injuries. Hearing loss can occur, which has implications ranging from communication difficulties to various health issues such as tinnitus and poor mental health.
Exposure to high noise levels can lead to noise-induced hearing loss (NIHL), an irreversible problem. This type of hearing damage may occur from one-off excessive noise exposure or exposure to noise above the recommended safe limits over time. Occupational NIHL is a widespread yet preventable problem.
Some of the most high-risk industries for NIHL include transportation, manufacturing, forestry and agriculture, mining, and oil and gas. Each sector has unique noise-related hazards, but the good news is that employers can take plenty of practical steps to decrease noise exposure in the workplace and keep workers safe.
Identify Noise-Related Hazards in the Workplace
The first step in managing occupational noise is identifying potential workplace noise-related hazards. These hazards can vary widely depending on the industry and specific job roles. It’s crucial to assess all areas of the workplace and tasks that could expose employees to excessive noise levels.
For instance, noisy machinery and equipment may pose significant risks in the manufacturing sector. Vehicle engines and road noise could contribute to elevated noise levels in the transportation industry. By conducting thorough assessments and involving employees in hazard identification, employers can gain valuable insights into potential sources of noise exposure.
Conduct a Noise Assessment to Assess the Risks
Once you identify potential noise hazards, conducting a comprehensive noise assessment is essential. This assessment involves measuring noise levels across different workplace areas using specialized equipment (for example, a sound level meter). The goal is to quantify the extent of noise exposure and determine whether it exceeds recommended safe limits.
For example, construction industry employers should measure noise levels from equipment and activities such as drilling, hammering, and heavy machinery operations. This data helps them make informed decisions about implementing effective noise control measures.
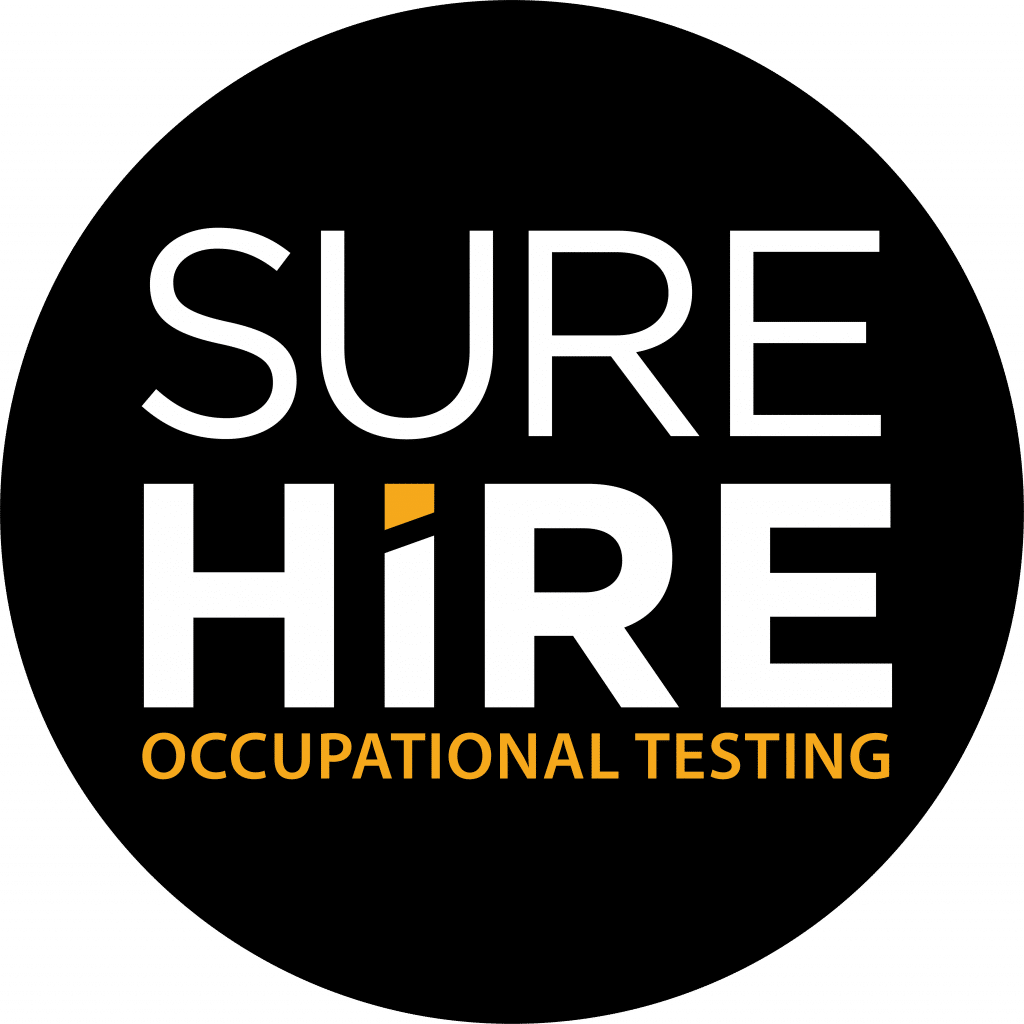
Request a Quote Today!
SureHire offers Audiometric Testing both in-facility and through our mobile fleet. Contact us today to request a quote!
Engineering Controls: Equipment Modification or Replacement
Engineering controls focus on modifying or replacing equipment to eliminate or reduce noise at its source. This proactive approach can significantly lower noise exposure levels. For instance, installing noise-reducing enclosures or dampening materials around machinery in a manufacturing setting can effectively reduce noise emissions.
Equipping heavy machinery with quieter exhaust systems can reduce noise in the mining industry. Such modifications protect workers’ hearing and create a more comfortable and productive work environment.
Administrative Controls: Adjusting Workplace Protocols and Procedures
Implementing administrative controls involves adjusting workplace protocols and procedures to minimize noise exposure. Employers can schedule noisy tasks during specific hours to limit employees’ time in noisy areas and create designated quiet zones.
For example, in a call center environment, provide employees with noise-canceling headphones to mitigate the impact of background noise during phone conversations.
Use Hearing-Related Personal Protective Equipment (PPE)
Personal protective equipment (PPE) designed to protect employees’ hearing is another essential component of managing occupational noise. Earplugs and earmuffs are types of PPE for reducing noise exposure to safe levels.
Providing comfortable and effective ear protection is crucial in any industry with high noise levels. Proper training on correctly using hearing-related PPE ensures that employees receive the intended protection.
Ensuring proper personal protective equipment (PPE) fit is paramount to its effectiveness. Ill-fitting hearing-related PPE can compromise its ability to adequately reduce noise exposure, rendering it less effective in safeguarding employees’ hearing.
This concern has been particularly relevant for women, as standard PPE sizes and designs have often been based on male anatomical proportions, potentially resulting in inadequate protection for female workers. Addressing this issue by providing PPE options accommodating diverse body types and conducting Hearing Protection Fit Testing can significantly enhance all employees’ overall safety and well-being.
Employers must consider several crucial factors beyond fit when selecting the right hearing protection. While a proper fit is essential to ensure optimal noise reduction, comfort is also important. Uncomfortable or cumbersome hearing protection may discourage employees from wearing it consistently, exposing them to potential risks. Noise reduction ratings (NRR) are also critical, with higher NRR values indicating more effective noise reduction.
The nature of the job and specific noise sources also determine the most suitable hearing protection. Whether custom molded earplugs or earmuffs are preferred, the chosen type should align with the work environment and tasks to provide reliable and comfortable noise attenuation, ultimately contributing to a safer and healthier workplace.
Conduct Regular Audiometric Testing
Regular audiometric testing, also known as hearing tests, is vital to a comprehensive hearing conservation program. These tests assess employees’ hearing over time and help detect changes that may indicate early signs of hearing loss.
For instance, in the aviation industry, where aircraft noise is a prevalent hazard, pilots and ground crew members should undergo regular audiometric testing. Early identification of hearing loss allows for timely intervention and adjustments to noise control measures.
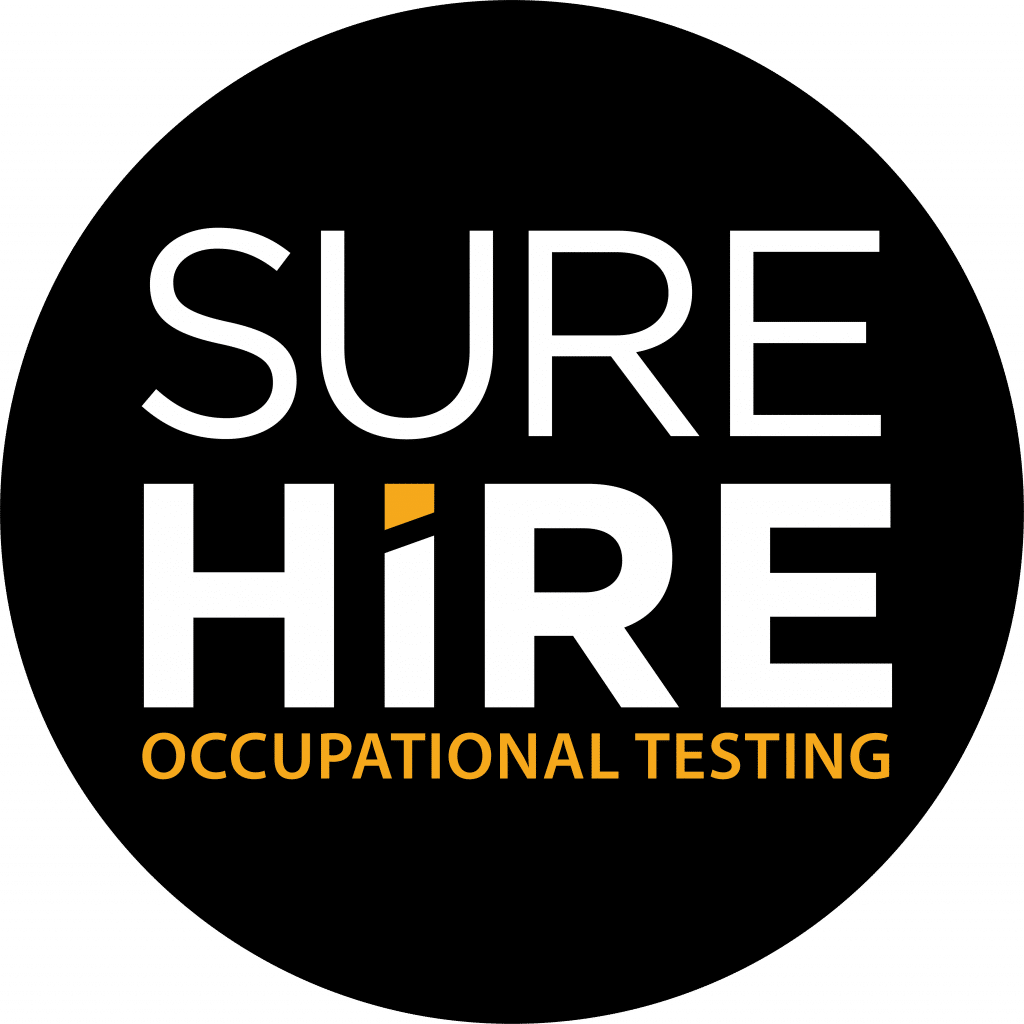
Request a Quote Today!
SureHire offers Audiometric Testing both in-facility and through our mobile fleet. Contact us today to request a quote!
Hearing Conservation Basics | In Conclusion
Effectively managing occupational noise is a critical responsibility for employers across various industries. The consequences of noise-induced hearing loss can be profound, affecting the well-being of employees and an organization’s overall productivity.
Employers can create a safer and more conducive work environment by identifying noise-related hazards, conducting thorough noise assessments, implementing engineering and administrative controls, providing appropriate PPE, and conducting regular audiometric testing. Taking proactive steps to mitigate noise risks demonstrates a commitment to the health and safety of the workforce, promoting a culture of prevention and protection.
Remember, safeguarding employees’ hearing is a legal requirement in many jurisdictions and a fundamental ethical responsibility. By prioritizing hearing conservation, organizations can ensure the long-term health and well-being of their most valuable asset—their employees.
You May Also Be Interested In…
- Do You Have Reasonable Suspicion?Employers cannot initiate reasonable suspicion testing without first going through the 5-step process. Reasonable suspicion training provides critical information about how to initiate reasonable suspicion testing, including the 5-step process and other tools that employers can use to help manage the misuse of alcohol and drugs in the workplace.
- An Employer’s Guide: What You and Your Employees Need to Know About DOT Drug & Alcohol TestingWhen implementing or maintaining DOT Drug & Alcohol testing, there are key areas that employers should consider.
- SureHire Occupational Testing Acquires COHR Health: A Positive Step Towards Safe, Healthy, Productive Workforces and CommunitiesWe are thrilled to announce that today, May 6, 2024, SureHire Occupational Testing has officially acquired COHR Health, a well-known leader in occupational health services. Read on…
- Occupational Testing Use Case – MiningIn this case study, we will explore how mining companies can use various types of occupational tests to reduce Total Recordable Incident Rates (TRIR) long term.
- 9 Strategies to Keep Workers Cool on Drilling Sites During Hot Summer MonthsThis article delves into strategies to keep workers cool and safe on drilling sites during the hot summer months.
- Hearing Conservation Basics: How to Manage Occupational NoiseLearn how to proactively mitigate occupational noise risks and help prevent NIHL among workers.